News
The Path to Biogas Expertise
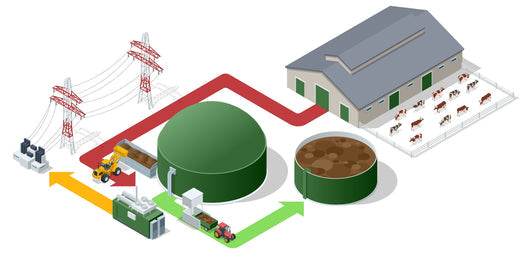
By Shane Marrs
Biogas production offers a sustainable solution for converting organic waste streams like food scraps, manure, and wastewater, into a valuable renewable energy source. This process relies on anaerobic digestion, where specialized microbial communities break down organic matter in the absence of oxygen.
Key Stages of Anaerobic Digestion:
-
Hydrolysis: In the initial stage, specialized bacteria break down complex organic matter into simpler compounds like sugars, fatty acids, and amino acids. This process involves the breaking of chemical bonds in complex molecules using water. It is similar to the process of digestion in the human body, where food is broken down into smaller, more easily digestible molecules.
-
Acidogenesis: These simpler compounds are further broken down by acidogenic bacteria into short-chain volatile fatty acids (VFAs). This process involves the fermentation of sugars and other carbohydrates into organic acids, such as acetic acid, propionic acid, and butyric acid.
-
Acetogenesis: Acetogenic bacteria then convert these VFAs into acetate, carbon dioxide, and hydrogen. This process involves the conversion of organic acids into acetate, a key intermediate in the production of methane.
-
Methanogenesis: Finally, methanogenic bacteria utilize these building blocks to create methane gas, the main ingredient in biogas. This process involves the conversion of acetate, carbon dioxide, and hydrogen into methane gas by a group of specialized bacteria called methanogens.
Critical Factors for Optimal Biogas Production:
-
Temperature Control: Maintaining a stable temperature within the digester is the most crucial factor for optimal microbial activity. Different microbial communities have specific temperature ranges for optimal performance, and maintaining the correct temperature ensures efficient breakdown of organic matter and biogas production. Most digesters are happiest and optimally productive within a temperature range of 95-131 degrees Fahrenheit (35-55 degrees Celsius). While fermentation generates some heat, external heat sources, such as hot water heat exchangers or steam injection, may be necessary to maintain this ideal temperature
-
pH Control: A stable pH range (typically 6.5-8.0) is essential for the efficient growth and activity of the microbial communities. pH fluctuations can inhibit microbial activity and reduce biogas production.
-
Mixing: Regular mixing ensures even distribution of organic matter within the digester, preventing settling and promoting efficient microbial contact. Adequate mixing is important, but excessive mixing can negatively impact microbial activity.
Control Systems:
-
Advanced Monitoring and Automation: Large-scale digesters often utilize sophisticated control systems that continuously monitor and adjust key parameters (temperature, pH, mixing) to optimize biogas production. These systems employ a variety of sensors and actuators to collect data on the digester's performance and make real-time adjustments as needed. For example, temperature sensors can be used to monitor the temperature of the digester contents, and heaters or coolers can be activated to maintain the optimal temperature range. pH sensors can be used to monitor the pH level of the digester contents, and acid or alkali can be added to adjust the pH as needed. Mixing systems, such as agitators or pumps, can be used to circulate the digester contents and ensure even distribution of organic matter. These systems may also include advanced features such as data logging, remote monitoring, and predictive maintenance capabilities.
-
User-Friendly Controls for Smaller Digesters: Smaller digesters may utilize simpler control systems, such as programmable logic controllers (PLCs), for easier operation and maintenance. These systems can be configured to monitor key parameters and trigger alarms or automatic adjustments to maintain optimal conditions. For example, a PLC can be programmed to automatically adjust the temperature or mixing rate based on sensor readings. This can help to ensure consistent biogas production and reduce the need for constant manual monitoring and intervention.
Taking Advantage:
To fully realize the benefits of biogas, we must continue to support research and development, which are essential to improve biogas production technologies and reduce costs. We must also encourage the adoption of sustainable waste management practices and support policies that incentivize biogas production. Lastly, we must promote the development and deployment of innovative technologies to enhance biogas production efficiency and reduce environmental impact. By working and learning together, we can unlock the full potential of biogas and create a more sustainable future.
Contact us to learn more about biogas systems and analyzers.